Advanced Metal Stamping Techniques for Precision Production
Advanced Metal Stamping Techniques for Precision Production
Blog Article
Unleashing the Possible of Metal Stamping: Specialist Tips and Finest Practices Revealed
In the realm of metal stamping, where precision and efficiency preponderate, the quest to maximize procedures and unlock covert capacities is a perpetual search. Know-how sharpened over years of market experience, incorporated with sophisticated innovations and innovative practices, holds the key to accomplishing exceptional outcomes. As we navigate with the intricate world of steel marking, a more detailed consider the ins and outs of tooling style, material option, manufacturing performance, quality assurance, and emerging fads promises a bonanza of insights waiting to be uncovered. Keep tuned to discover just how these professional suggestions and finest practices can reinvent the steel stamping landscape.
Tooling Style Optimization
Enhancing tooling design is important for improving efficiency and precision in steel marking procedures. A well-balanced tooling style can dramatically influence the quality and cost-effectiveness of steel stamping operations. By carefully taking into consideration elements such as product choice, die arrangement, and component geometry, producers can enhance manufacturing procedures and enhance general item high quality.
One trick facet of tooling style optimization is picking the most ideal products for the punches and passes away made use of in the stamping process. Products with high wear resistance and sturdiness are preferred to make certain long life and decrease tooling maintenance requirements. In addition, die configuration plays a vital duty in accomplishing harmony and consistency in stamped components. Correct die layout can assist avoid problems such as wrinkling, tearing, and too much springback, resulting in higher manufacturing yields and reduced scrap rates.
Furthermore, maximizing component geometry through tooling design can aid minimize product waste and production time. By very carefully forming passes away and punches to match the wanted component specs, manufacturers can achieve tighter resistances and boosted part high quality. Generally, spending time and resources in optimizing tooling design can lead to significant lasting benefits for metal marking procedures.

Material Selection Approaches
Strategically choosing materials for metal stamping tooling is critical for guaranteeing sturdiness and efficiency in making procedures. When choosing products for metal marking applications, several key factors must be considered. The first factor to consider is the sort of material being marked. Various materials, such as light weight aluminum, stainless steel, or copper, need specific tooling products to guarantee ideal efficiency and long life.
Another critical consider product choice is the expected production volume - Metal Stamping. For high-volume manufacturing runs, tooling products with superior wear resistance and durability, such as tool steels or carbide, are frequently chosen to stand up to the roughness of continuous stamping procedures
Moreover, the complexity of the marking style and the needed precision likewise play a substantial duty in product choice. For complex marking patterns or tight tolerances, products with high thermal conductivity and excellent machinability, like beryllium copper or device steel alloys, may be better to accomplish the desired outcomes.
Production Effectiveness Strategies
To enhance making result and minimize production costs, applying reliable methods in metal stamping procedures is vital. One crucial strategy for boosting production efficiency is purchasing automation. Automated metal marking makers can carry out tasks with precision, consistency, and at a much faster price than manual work, bring about boosted productivity and lowered cycle times. Furthermore, implementing anticipating maintenance practices can assist avoid unexpected downtime by identifying possible equipment failures before they happen. By on a regular basis monitoring maker efficiency and addressing issues proactively, suppliers can enhance production routines and decrease disturbances.
One more strategy to improve manufacturing effectiveness is through constant procedure improvement. Conducting normal audits and efficiency examinations can assist identify traffic jams, site web inadequacies, and locations for enhancement within the metal marking process. By analyzing information and comments from these assessments, makers can apply targeted remedies to streamline procedures, rise throughput, and optimize general efficiency.
In addition, taking on lean manufacturing concepts, such as 5S method and Kanban systems, can aid eliminate waste, improve workflow, and improve overall performance in metal marking procedures. By cultivating a culture of continuous renovation and empowering employees to add ideas for performance gains, suppliers can open the complete possibility of their steel marking processes.
Top Quality Control Measures
Structure on the foundation of reliable manufacturing methods in steel stamping procedures, guaranteeing strict high quality control procedures is crucial for maintaining item standards and consumer complete satisfaction. Quality control in steel marking involves systematic evaluation, screening, and tracking of the manufacturing refines to identify and correct any kind of variances or flaws that could jeopardize the last product's stability (Metal Stamping). Carrying out steps such as normal equipment upkeep, in-process assessments, and complete testing of completed components can aid find issues early and prevent expensive rework or product recalls
Regular audits and evaluations of quality procedures can assist determine locations for improvement and ensure uniformity in product top quality. By fostering a society of quality consciousness amongst staff members and giving sufficient training on quality control treatments, makers can boost total product integrity and brand credibility.
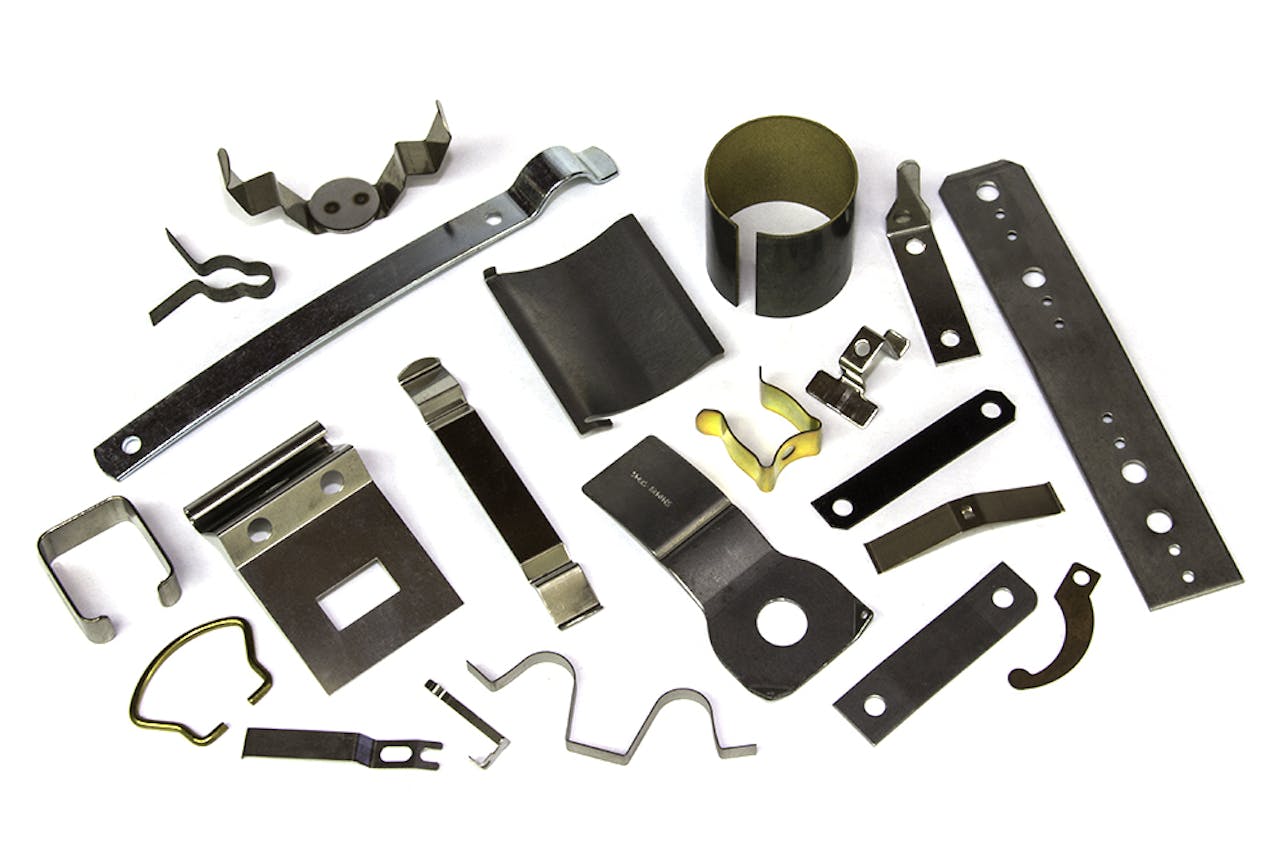
Cutting-edge Steel Stamping Technologies
Advancements in steel marking modern technologies have actually revolutionized the production market, enhancing effectiveness and precision in the manufacturing procedure. Servo presses offer unparalleled control over the marking process, allowing for changes in dwell, speed, and pressure time with phenomenal precision.
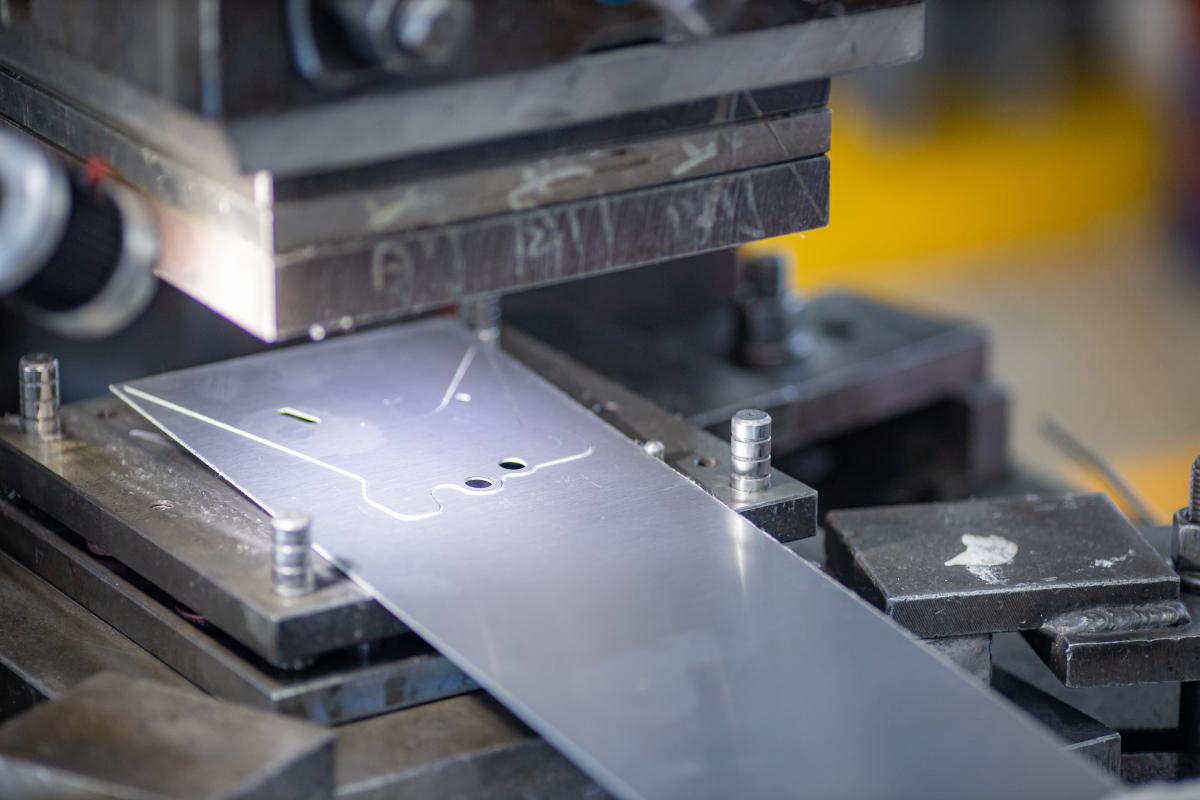
Additionally, the fostering of additive production methods in steel marking, such as 3D printing of die components, has streamlined the tooling style and manufacturing procedure. This strategy enables greater layout flexibility, fast prototyping, and cost financial savings in tooling manufacturing. By leveraging these cutting-edge innovations, producers can open brand-new degrees of performance, quality, and competition in the metal stamping industry.
Conclusion
Finally, the optimization of tooling style, strategic material selection, efficient production techniques, quality control steps, and innovative modern technologies are vital for unleashing the complete capacity of steel stamping. By executing these best methods and professional pointers, read the full info here makers can enhance performance, increase top visit quality, and remain affordable in the steel stamping sector. It is critical for firms to continually evaluate and boost their processes to attain success in this area.
As we browse through the complex globe of metal stamping, a more detailed look at the ins and outs of tooling layout, product selection, production performance, high quality control, and emerging fads guarantees a treasure chest of insights waiting to be discovered. A well-balanced tooling design can considerably influence the high quality and cost-effectiveness of steel stamping operations.Building on the structure of efficient production methods in steel marking processes, guaranteeing strict high quality control measures is important for maintaining item criteria and consumer complete satisfaction. Quality control in metal marking entails systematic inspection, testing, and tracking of the production processes to determine and correct any variances or problems that could compromise the last item's honesty.In conclusion, the optimization of tooling style, calculated product option, reliable manufacturing methods, high quality control measures, and ingenious innovations are vital for letting loose the full possibility of metal marking.
Report this page